کوپلینگ بسیار الاستیک کِگِل فلکس
این کوپلینگ ها با خاصیت بالای الاستیک و مطابق شکل 16-7 دارای عضو رابط مخروطی شکل (a) هستند. حداکثر گشتاوری که می توانند منتقل کنند 3500 نیوتن متر است. و قطر شفاف آن می تواند ماکزیمم 450 میلی متر باشد.
کلاچ ها
کلاچ ها، اجزایی از ماشین هستند که در هنگام نیاز، ارتباط یک محور را به محور دیگری برقرار یا قطع می کنند. و سرعت های آن دو محور را به یک سرعت واحد می رسانند. همچنین با گشتاور ایجادی، انرژی را منتقل می سازند.
ابعاد کلاچ ها متناسب با قطر محورها به صورت استاندارد تولید می شود. و مکانیزم ارتباطی آنها دارای اهمیت زیادی است. در موقع درگیری، حتماً باید محورها به صورت هم مرکز قرار گیرند. در کلاچ ها معمولاً ارتباط به صورت مکانیکی یا الکترومغناطیسی برقرار می شود. به همین دلیل آنها در کلاچ های مکانیکی و الکترومغناطیسی می نامند. در کلاچ های مکانیکی، ارتباط بسیار ساده است. و به صورت تماسی یا اصطکاکی برقرار می شود. به همین دلیل، کلاچ های مکانیکی به دو گروه خشک و اصطکاکی تقسیم می شوند.
کلاچ های متغیر، علاوه بر فراهم سازی امکان انتقال حرکت و گشتاور، وظیفه دارند حرکت را نیز به دلخواه قطع و وصل کنند. از برخی کلاچ ها به منظور ضامن ایمنی نیز استفاده می شود. بدین صورت که در موقع افزایش غیر مجاز نیرو، ارتباط حرکت را قطع می کنند. و مانع از آسیب دیدگی سایر اجزاء ماشین می شوند. ضمناً به وظیفه اصلی خودشان نیز عمل می کنند. حال بعضی از کلاچ ها را به اختصار شرح می دهیم.
کلاچ های مکانیکی
این کلاچ ها در مواقع دلخواه، حرکت بین دو محور محرک و متحرک را قطع و وصل می کنند. این ارتباط با عمل مکانیکی یا الکترومغناطیسی اتفاق می افتد و به همین دلیل کلاچ های مکانیکی یا الکترومغناطیسی وجود دارند.
در شکل 17-7 ب نیمه a کلاچ بر روی محور محرک ثابت شده است. و نیمه b آن روی محور متحرک قرار می گیرد. به طوری که بتوانیم نیمه b کلاچ را در جهت محور بلغزانیم. در نتیجه لغزش، با نیمه a ارتباط برقرار می کند. حرکت محور محرک به محور متحرک منتقل می شود. و ارتباط ان دو برقرار می شود. و در صورت جدا شدن نیمه b از نیمه a، حرکت دو محور از همدیگر جدا می شود.
ارتباط در کلاچ های مکانیکی به وسیله اجزای تماسی آنها و یا به کمک اصطکاک برقرار می شود. ضمناً تمامی این کلاچ ها در نوع اتوماتیک نیز موجود هستند. در شکل 18-7 سیستم قطع و وصل کننده مکانیکی ساده ای را مشاهده می کنید. که با عمل دو طرفی، حرکت کلاچ ها را قطع و وصل می کند. این سیستم در وسایل نقلیه موتوری زیاد کاربرد دارد.
کلاچ ها ی خشک قفلی
مکانیزم این نوع کلاچ ها خیلی ساده است. و به شکل های پنجه ای و دنده ای ساخته می شوند. همانطور که در شکل 19-7 می بینید. در سطح پیشانی این نوع کلاچ ها، پنجه هایی وجود دارد. که در هنگام درگیری، با پنجه های نیمه دیگر کلاچ ارتباط برقرار می کنند.
در نتیجه ارتباط سطوح پنجه ها به یکدیگر، گشتاور انتقال می یابد. پنجه ها معمولاً به شکل های مکعب مستطیل (19-7الف)، فرم دار (19-7ب) و دنده ای (19-7پ) ساخته می شوند.
معمولاً کلاچ های قفلی، در سرعت های مختلف، می توانند ارتباط دو محور محرک و متحرک را قطع کنند. اما در حالت بی حرکت یا در سرعت های کم نیز می توانند. ارتباط را برقرار سازند. کلاچ هایی که پنجه های شیب دار (زاویه ای) دارند تا RPM 150 می توانند، درگیر شوند. فقط کلاچ های پنجه ای فرم دار (شکل 19-7 ب) گشتاور را در یک جهت تغییر می دهند.
کلاچ های دارای پنجه مکعب مستطیل (شکل 19-7 الف) می توانند گشتاور را در هر دو جهت منتقل کنند. در مواردی که محور محرک در حال حرکت نیست، یا هر دو نیمه کلاچ دارای یک سرعت و در حال حرکت باشند.. می توانند ارتباط را برقرار سازند (شکل 20-7 الف).
کلاچ های دارای پنجه مکعب مستطیل (شکل 19-7الف) می توانند گشتاور را در هر دو جهت منتقل کنند. در مواردی که محور محرک در حال حرکت نیست. یا هر دو نیمه کلاچ دارای یک سرع و در حال حرکت باشند. می توانند ارتباط را برقرار سازند (شکل 20-7 الف).
در کلاچ های دنده ای، دندانه ها، یا در سطح جانبی نیمه کلاچ ها (شکل 20-7). و یا در سطح پیشانی آنها قرار دارند (شکل 20-7پ).
این کلاچ ها تا 300 دور بر دقیقه می تواند درگیر شوند. معمولاً کلاچ ها صلب در ابعاد کوچک می توانند گشتاورهای بسیار بزرگی را منتقل کنند. فقط در موقع ارتباط، دو نیمه کلاچ با ضربه (ضربه های کلاچی) رو به رو می شوند. به همین دلیل باید نیمه های کلاچ به طور کامل هم مرکز باشند.
کلاچ اصطکاکی
برای ارتباط دو نیمه کلاچ، نیمه کلاچ موجود بر روی محور محرک، با یک نیروی محوری بر روی نیمه کلاچ دیگر نیرو وارد می کند. در روی دو سطح تماس، یک نیروی اصطکاکی و همچنین گشتاور اصطکاکی حاصل می شود. و با این فرآیند حرکت منتقل می شود.
کلاچ های اصطکاکی
در کلاچ های اصطکاکی، حرکت محور محرک به محور متحرک، از طریق نیرو، با اصطکاک امکان پذیر است. مزیت مهم کلاچ های اصطکاکی این است که در حین حرکت می توانند. درگیر و یا آزاد شوند و گشتاور چرخشی آنها به واسطه نیروی اصطکاک محدود است. به همین خاطر بسیار نرم کار می کنند. و هم زمان به عنوان کلاچ های ایمنی به کار می آیند.
سیستم های کنترل انواع ماشین های ساخت و تولید امروزی دارای کلاچ های اصطکاکی هستند. به خصوص بعضی از آنها که از راه دور قطع و وصل می شوند. جایگاه بالایی در صنعت امروز پیدا کرده اند. نیروی قطع و وصل این کلاچ ها به کمک هوای فشرده، روغن پرسی و یا به صورت مغناطیسی ایجاد می شود. در شکل 21-7 یک نوع کلاچ اصطکاکی دیده می شود.
این کلاچ ها ویژگی هایی به شرح زیر دارند.
الف) در زمان شروع ارتباط دو نیمه کلاچ و تماس آنها، در سطوح اصطکاک یک لغزش به وجود می آید. بعد از درگیر شدن دو نیمه کلاچ، این لغزش از نظر تئوری صفر می شود. و هر دو محور با یک سرعت شروع به حرکت دورانی می کنند.
ب) در نتیجه این لغزشف اتلاف انرژی و به دنبال آن ازدیاد گرما ظاهر می شود. عمل قطع و وصل هرچه بیشتر تکرار شود. باعث به وجود آمدن ساییدگی و ایجاد خراش می شود.
پ) گشتاور به راحتی از محور محرک به محور متحرک (بدون ضربه) انتقال می یابد.
ت) عمل قطع و وصل در هر زمان خیلی ساده و راحت انجام می گیرد. با توجه به بند پ و ت، کلاچ های اصطکاکی در عمل، بیشترین مصرف را دارند. در صنایع اتومبیل و ماشین سازی افزار مورد مصرف زیادی دارند.
کلاچ های اصطکاکی با در نظر گرفتن شکل سطح تماس آنها به صورت های دیسکی، مخروطی، کفشکی و نواری ساخته می شوند.
در شکل 22-7 نمونه ساده این نوع کلاچ ها را مشاهده می کنیم. کلاچ های اصطکاکی به صورت های اتوماتیک نیز زیاد ساخته می شوند. که نمونه هایی از آنها را شرح خواهیم داد.
کارکرد
گشتاور چرخشی در هر دو جهت توسط اصطکاک لنت کلاچ که به صفحه فولادی متصل است. منتقل می شود. این صفحه قابل لغزش روی هزارخار امتداد محور شماره (2) جعبه دنده و قابل جابه جا شدن در امتداد محور است. لنت کلاچ به وسیله فنرهای فشاری (3) بین دو صفحه فشار (4) فشرده می گردد. و با محفظه کلاچ (5) اتصال اصطکاکی به وجود می آید. با لغزش غلاف (6) به کمک اهرم کلاچ (7) سمت چپ انتقال حرکت قطع می شود. بنابراین عمل حلقه متصل به بلبرینگ (8) قسمت کروی انتهای اهرم های (9) را فشار می دهد..و سر دیگر اهرم، موجب حرکت صفحه کلاچ به راست و جمع شدن فنرهای فشار و قطع اتصال کلاچ می شود.
کلاچ های یک صفحه ای
در شکل 23-7 یک کلاچ دیسکی یک صفحه ای که برای قطع و وصل حرکت در وسایل نقلیه موتوری مناسب است، مشاهده می شود.
طرز کار کلاچ صفحه ای را در شکل 24-7 می بینیم. با دقت در این شکل، کلاچ های صفحه ای را در حالت کار کردن و همچنین در حالت آزاد مشاهده می کنیم. اگر اهرم را در جهت فلش بکشیم (شکل 24-7الف) کلاچ درگیر می شود و کار انجام می دهد. ولی اگر آن را به جای اول خود برگردانیم (شکل24-7ب) کلاچ آزاد می شود.
در شکل 25-7 نیز کلاچ صفحه ای نوع دیگری را مشاهده می کنیم. که در شکل 25-7 در حالت درگیر و در شکل 25-7 پ در حالت آزاد، نمایان و مشخص است.
کلاچ های چند صفحه ای
یک کلاچ چند صفحه ا، در شکل 26-7، نمایان و مشخص است. این نوع کلاچ ها از نظر ساختمان نظیر کلاچ های یک دیسکی هستند. با این تفاوت که در اینجا به بدنه محور محرک و همچنین به گلویی محور متحرک، دیسک های زیادی بست می شوند. از طرف دیگر دیسک ها بدون پوشش هستند. و از فولادهای مورد سخت کاری تولید می شوند. در این صورت، سطوح اصطکاکی فولاد-فولاد هستند. این کلاچ ها به کلاچ های سینوسی نیز مشهورند. و بین دیسک ها، ورق های فنری خیلی نازکی مورد کاربرد می باشد (شکل 26-7 ب).
این فنرها باعث می شوند. تا کلاچ تدریجاً و به راحتی قطع و وصل شود. فنرها در هنگام برقراری ارتباط، باعث می شوند. که در سطوح تماس، فشار افزایش یابد. این فشار باعث می شود گشتاور اصطکاکی نیز به تدریج زیاد شود. در کلاچ هایی که سطوح تماس آنها فولاد -فولاد معمولی تولید شدند. روغن موجود بین دیسک ها باعث چسبیدگی آن دو به یکدیگر می شود. در این شرایط هرگاه نیروی فشار را برداریم. صفحات به راحتی از هم جدا نمی شوند. به همین دلیل وجود فنرها در لابه لای صفحات، سبب می شود. که دیسک ها به راحتی از هم جدا شوند.
کلاچ های مخروطی
در شکل 27-7، کلاچ مخروطی یک صفحه ای ساده را مشاهده می کنیم. با کلاچ های مخروطی یک صفحه ای می توانیم گشتاورهای کوچک را انتقال دهیم. برای انتقال گشتاورهای چرخشی بزرگ که نیروی محوری نیز افزایش می یابد. از کلاچ های مخروطی دوبل استفاده می شود. کلاچ مخروطی شکل 27-7 در سیستم ترمز نیز به کار می رود.
کارکرد
کلاچ مخروطی دوبل
در این کلاچ، حرکت از طریق اصطکاک دو سطح مخروطی (2) و (3) منتقل می شود. پین (4) در روی گلویی (1) تثبیت شده است. و در دو سطح نیز روی همین پین در امتداد محوری لغزش می کنند. در اثر لغزش غلاف (5)، عمل قطع و وصل صورت می گیرد.
ترمزها
ترمزها اجزایی از ماشین هستند که سرعت حرکت اجسام را کم کرده، یا آنهارا به طور کلی از حرکت باز می دارند. و برای این کار انرژی جنبشی یا انرژی پتانسیل را در طی مراحل کاهش سرعت یا توقف کامل قطعه متحرک جذب می کنند. این انرژ جذبی به صورت حرارت تلف می شود. انجام هرچه بهتر عمل ترمز، به فشار ایجادی در واحد سطح ترمز. ضریب اصطکاک و قابلیت ترمز اتلاف حرارت که معادل انرژی جذبی می باشد، بستگی دارد. ترمزها مشابه کلاچ ها هستند. با این تفاوت که کلاچ ها دو جزء در حال حرکت را به هم وصل می کنند. در حالی که ترمزها یک جزء متحرک را به قاب متصل می سازند.
ترمزها با توجه به عملکردشان انواع مختلفی دارند. رایج ترین آنها ترمزهای مخروطی، یک صفحه ای، دو صفحه ای، چند صفحه ای، کفشکی یا کفشک های داخلی یا خارجی، دیسکی و نواری هستند.
همچنین سیستم های کنترل آنها مانند کلاچ ها به صورت مکانیکی، پنوماتیکی، هیدرولیکی و الکترومغناطیسی تولید می شوند. ترمزها را برای منظورهای مختلفی به کار می برند. مثلاً برای پایین آوری جسمی که سیستم ترمز آن انرژی پتانسیل را حذف کرده و به صورت انرژی حرارتی تبدیل می کند. و یا در جسمی مانند خودروها، انرژی جنبشی را به صورت انرژیی حرارتی تلف می کند. و باعث توقف آن می شود. یا جسمی مثل آسانسورر و جرثقیل را در حالت آویزان نگه می دارد. در شکل 29-7 یک مدل از ترمزهای مخروطی را مشاهده می کنید. که یک موتور روتور کشویی با ترمز مخروطی مربوط است.
کارکرد
در حالت سکون، فنر (e) از طریق بلبرینگ (f) و دیسک (c) ترمز را به مخروط ترمز در محفظه (d) فشار می دهد. و در نتیجه شافت b محکم نگه داشته می شود.
با جریان برق، روتور (a) در اثر نیروی مغناطیسی به درون استاتور مخروطی h کشیده می شود. و بدین ترتیب ترمز رها می شود. در اثر قطع جریان برق، فنر ترمز را به کار می اندازد. و فنرهای بشقابی (i) ضربات محوری را مستهلک می کنند.
ترمزهای کفشکی
در ترمزهای کفشکی که موارد استفاده زیادی دارند. کفشک های ترمز مجهز به لنت های خیلی با دوام هستند. در شکل 30-7 یک نمونه از این ترمزها که یک کفشکی داخلی و خارجی هستند. و در صنعت خودروسازی کاربرد زیادی دارند، نمایان و مشخص است.
کارکرد
ترمزهای کفشکی: به طور کلی از سه قسمت تشکیل می شوند. لنت ترمز (1) که روی قطعه فولادی به فرم نیم دایره نصب است. کفشک (3) نام دارد. چرخ (2) مربوط به ترمز است. و در نتیجه ایجاد فشار کفشک از داخل و یا خارج به چرخ عمل ترمز صورت می گیرد. بازوی ترمز، وظیفه وارد کردن نیرو به کفشک را به عهده دارد (شکل 30-7 الف).
ترمزهای دو کفشکی، به ویژه در شرایط کاری سخت، مثلاً در جرثقیل هاف سیستم های انتقال مواد و سیستم های نوردکاری به کار می روند. در شکل 31-7 یک ترمز دو کفشکی را مشاهده می کنید که در جرثقیل به کار می رود.
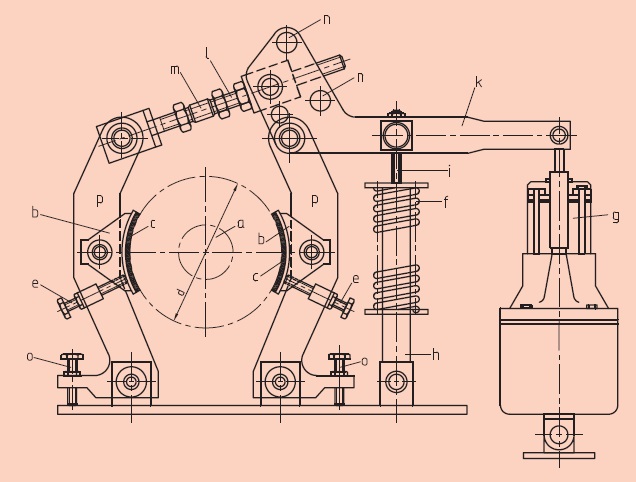
شکل 31-7 ترمز دو کفشکی خارجی به عنوان ترمز ایست کننده
(a) شافت موتور، (b) کشفک های ترمز (c) لنت ترمز است. کفشک ها با پین در اهرم ترمز (p) یاتاقان بندی می شوند. و پیچ های تنظیم (e) از واژگون شدن کفشک ها در اثر وزنشان، در حالتی که ترمز آزاد است، جلوگیری می کنند. فنر فشاری (f) اهرم ترمز را همراه با کفشک ها از طریق میله های (K,i,h,l) به طبلک ترمز فشار می دهد. (g) دستگاه هیدرولیک یا آهنربای کششی است. برای خلاصی ترمز از طریق (k,l) عمل می کند. (m) مهره تنظیم نیروی فنر است. (n) سوراخ تنظیم درجه تبدیل اهرم است. نهایت (o) پیچ تنظیم (فنر تنظیم) حد اهرم در هنگام خلاصی ترمز و به منظور قرار گیری یکسان کفشک ها به کار می رود. پیچ های تنظیم نباید در کورس آهنربا مانع ایجاد کنند.
ترمزهای طبلکی که در گذشته در چرخهای خودرو به کار می رفتند. ترمزهایی با کفشک های داخلی هستند. که در آنها کفشک های ترمز از داخل به طبلک ترمز (کاسه ترمز) فشرده می شوند. امروز به جای آنها از ترمزهای دیسکی استفاده می شود. که ساختمان ساده تری دارند. ترمزهای دیسکی گرما را بهتر هدایت می کنند. و به خصوص در برابر ضریب اصطکاک حساس نیستند. در شکل 32-7 ترمز دیسکی با زین ثابت نمایان و مشخص می باشد. که به انبر نیز معروف است.
در دیسک ترمز یک کاسه ترمز با کفشک های داخلی قرار دارد. این ترمز طبلکی به عنوان ترمز دستی عمل می کند. در داخل زین دو سیلندر ترمز مقابل یکدیگر قرار می گیرند. یکی از سیلندرها در محفظه فلانچ و دیگری در محفظه درپوش زین قرار دارد. زمانی که دیسک ترمز همراه با چرخ خودرو دوران می کند. زیر ترمز در حالت سکون خواهد ماند.
اجزاء یک زین را در شکل 33-7 مشاهده می کنید.
پیستون های هر دو سیلندر به اجزاء حامل لنت های ترمز اثر می کنند. و آنها نیز از دو طرف برعکس یکدیگر به دیسک ترمز فشار وارد می آورند. لنت ها در این ترمزها کوچک تر از لنت های ترمزهای طبلکی هستند. و به همین دلیل دماهای موضعی به وجود آمده، بالاترند. با وجود این هوای خنک می تواند به قسمت های پوشانده نشده دیسک ترمز از هر دو طرف جریان یابد. نیروی کاراندازی از ترمزهای طبلکی بزرگ تر است. از این رو در این ترمزها اغلب تقویت کننده های نیروی ترمز پیش بینی می شود.
اما ترمزهای دو کفشکی داخلی از نظر کارکرد مشابه ترمزهای کفشکی خارجی هستند. در خودروهای سواری و کامیون ها، از این ترمزها استفاده می شود. که بیشتر هیدرولیکی کار می کنند. به دلیل گشتاور اینرسی خودرو در زمان ترمز گرفتن. 55% الی 60% وزن خودرو به لاستیک های جلو گشتاور وارد می شود. در نتیجه، لاستیک های جلوی ماشین همیشه نسبت به لاستیک های عقب به اندازه 55% الی 60% به گشتاور نیروی اصطکاکی نیاز دارد. ترمزها بر مبنای مشخصات بالا و سیستم هیدرولیک آنها مطابق شکل 34-7 طراحی می شود. که به لاستیک های جلوی ماشین فشار زیادی را انتقال می دهند. از نظر عمل کردن، به صورت هماهنگ کار می کنند.
در شکل 35-7 مدار هیدرولیکی سیستم ترمز را می بینیم. در این تصویر نیروی وارد بر پدال ترمز به پیستون سیلندر اصلی منتقل می شود. پیستون، روغن را به فشار لازم به سیلندر داخل چرخ می فرستند و در آنجا فشار روغن باعث می شود. که کفشک ها از هم باز شوند. به کاسه چرخ بچسبند و در اثر اصطکاک به وجود آمده، سیستم ترمز کند.
البته این ترمزها با سیستم پنوماتیکی نیز موجود هستند. در این سیستم به جای روغن از هوای فشرده استفاده می شود. و کارکرد آن، مطابق عمل سیستم هیدرولیکی است. در شکل 36-7 مدار پنوماتیکی سیستم ترمز را مشاهده می کنید.
ترمزهای نواری
در این ترمزها یک نوار فلزی در اطراف فلکه قرار دارد. که اصطکاک ایجاد شده بین این نوار و چرخ، باعث توقف سیستم می شود. راندمان عمل ترمز، به زایه پیچش نوار در اطراف چرخ، ضریب اصطکاک و تنش موجود در نوار بستگی دارد.
یک ترمز نواری ساده در شکل 37-7 دیده می شود. این نوار طوری کشیده شده و به شاسی متصل شده که به حالت کاملاً کشیده درآمده است. یک نوع دیگر ترمز نواری در شکل 38-7 نشان داده شده است. در این ترمزها، چرخ در هر دو طرف می تواند حرکت و عمل کند. زیرا بازوهای گشتاور در هر دو طرف چرخ با هم برابر هستند.
لنت ها
لنت ها، در کلاچ ها و ترمزها کاربرد دارند. در ترمزها، پوشش کفشک ها را لنت ها تشکیل می دهند (شکل39-7).
جنس لنت ها با توجه به این که همیشه با اصطکاک و گرما رو به رو هستند. از اهمیت خاصی برخوردار است. لنت ها با توجه به اهمیت نوع کارشان، باید دارای ویژگی هایی باشند که چند مورد آنها را بیان می کنیم.
الف) ضریب مالشی بالا و یکنواختی داشته باشند.
ب) نفوذناپذیری آنها نسبت به شرایط محیط (رطوبت) در نظر گرفته شود.
پ) در برابر گرمای زیاد، توانایی پایداری داشته باشند و بتوانند گرما را به خوبی هدایت کنند.
ت) برگشت پذیری آنها خوب باشد.
ث) در مقابل سایش، خراش، ور آمدن یا باد کردن، مقاومت زیادی داشته باشند.
چنانچه ملاحظه می شود. ساخت مواد مالشی، یک فرآیند کاملاً تخصصی است. بنابراین لازم است که به انتخاب آنها توجه لازم را داشته باشیم. از بهترین نوع آنها و همچنین از استانداردهای موجود استفاده کنیم. لنت ها را در بیشتر ترمزها از مواد آزبست، بعنوان مواد اصطکاکی، می سازند. زیرا این مواد در مقایل اثرات حاصل از حرارت، مقاومت خوبی دارند.
آزبست را به صورت الیاف تاپ می دهند، و می بافند. سپس آن را به یک نوع ماده چسبی آغشته می کنند، حرارت می دهند. و تحت فشار به صورت یکپارچه در می آورند. کفشک های ریخته شده و لنت ها نیز بدون یافتن، مستقیماً از آزبست و ماده چسبی ساخته می شوند.
ضمناً لنت ها را از چوب، چرم، پنبه کوهی نسوز نیز می سازند. که به وسیله پیچ های سر خزینه ای یا پرچ به کاسه چدنی یا فولادی بسته می شوند. و یا آنها را با چسب های مخصوص می چسبانند. جنس چرخ ها علاوه بر چدن بر حسب احتیاج، از فولاد زنگ نزن و آلومینیوم نیز ساخته می شود.
شکل 40-7 سیستم ترمز یک ماشین را نشان می دهد. که لنت در داخل کاسه چرخ بر روی کفشک ها نصب شده است.
شرکت خشکه و فولاد پایتخت (( مدیریت : جواد دلاکان )) صنعتگران عزیز، افتخار داریم. که سی سال تجربه گرانبهای خویش را در زمینه عرضه انواع ورق آلیاژی. و انواع فولاد آلیاژی برای خدمت رسانی به شما هموطنان کشور عزیزمان ایران ارائه می دهیم. پیشاپیش از اینکه شرکت خشکه و فولاد پایتخت را جهت خرید خود انتخاب می نمایید سپاسگزاریم.ارتباط با ما:
۰۹۱۲۱۲۲۴۲۲۷
۰۹۳۷۱۹۰۱۸۰۷
تلفن: ۰۲۱۶۶۸۰۰۲۵۱
فکس: ۶۶۸۰۰۵۴۶
ارتباط با ما در شبکه های اجتماعی
https://t.me/foolad_paytakht تلگرام
https://www.instagram.com/folad_paytakht اینستاگرام
https://www.instagram.com/foolad_paytakht.ir اینستاگرام